Das wird ein umfassenderer Artikel. Der Artikel wird noch weiter vervollständigt.
Ich habe folgende Themen auf dem Programm:
Arduino Mega 2560-16
Ramps 1.4
Geetech Fullgraphic Smart Controller
Optische Endschalter
Pololu A4988 Schrittmotortreiber
Kabelwege
Arduino Mega 2560-16
Da gibts nicht viel dazu zu sagen, der wird einfach gekauft und dann hat man ihn.
Ach doch noch was: Der eingebaute Spannungsregler zum Erzeugen der 5V Betriebsspannung ist ein Linearregler, und der hat bei 12V schon arg zu kämpfen seine Verlustleistung loszuwerden. Der kann nicht aus dem 24V Netzteil versorgt werden. Bei meinem sainsmart Arduino Clone ist 12V für den Energiebedarf (da hängt ja auch noch der Smartcontroller und dessen Displaybeleuchtung mit auf der 5V Schiene) schon zu viel, da steigt er durch Strombegrenzung und Spannungsfall auf der 5V schiene langsam aus. Soll der Drucker ohne USB-Anschluß zum Hostcomputer von der SD-Karte drucken können, ist hier also ein externer Spannungsregler für 5V, oder die versorgung des Arduino-Board über die Hohlsteckerbuchse mit 7-10V notwendig, damit der Spannungsregler auf dem Arduino nicht überhitzt.
Wichtig: Bei Betrieb der Motortreiber/RAMPS mit 24V muss unbedingt die Diode unter dem Motortreiber ausgelötet werden, die die Spannung vom Ramps auf den Spannungsreglereingang des Arduino einspeist. Näheres findet sich im Reprap-Wiki zum Ramps 1.4.
Ramps 1.4
Ramps 1.4 ist ein Motortreiber-Aufsatz „Shield“ für den Arduino Mega. (Reprap Arduino Mega Pololu Shield).
Es können 5 Motortreiber aufgesteckt werden und zudem befinden sich hier noch die elektrischen Anschlüsse für Temperaturfühler, Heizbett, Extruderheizung, Kühl-Lüfter für das Druckstück und der Anschluß für das Heizbett und die Endschalter.
Die Pololu Motortreiber (bei Verwendung des A4988!) müssen mit dem Poti von den dicken Stromanschlüssen wegzeigen.
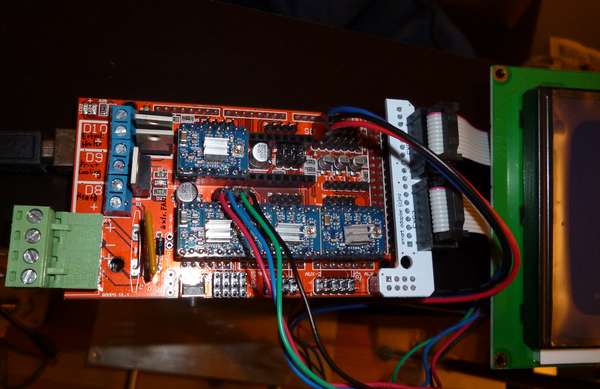
Auf der RAMPS-Platine muss bei Verwendung von 24V eine Diode ausgelötet werden. Der Heizbettanschluß kann nur 11A Schalten, die große Polyfuse ist nur für 16V geeignet und muss gegen ein 35V-Typ getauscht werden, oder durch etwas anderes (z.B. KFZ-Flachsicherung) ersetzt werden. Die FET sind nicht die allertollsten und können durch welche mit niedrigerem RDSon-Widerstand getauscht werden um höhere Ströme schalten zu können. Im Fall des Heizbett müssen dazu aber zusätzlich die Leiterbahnen verstärkt werden.
Damit alles korrekt funktioniert, müssen alle in der Firmware konfigurierten Temperaturfühler auch angeschlossen sein!
Anschluß der Motoren:
Der Anschluß der Schrittmotoren ist unklar, auf der Platine steht jedoch 1A, 1B, 2A, 2B an den Stiftleisten. Bei den Motoren entsprechend das Datenblatt hernehmen und die Anschlüsse 1A/1B jeweils einer Spule, und 2A/2B der anderen zuweisen, oder die zugehörigkeit der Leitungen zu den beiden Wicklungen einfach mit einem Widerstandsmeßgerät ermitteln. Durch drehen des Steckers kann nachher die Drehrichtung des Motores noch korrigiert werden.
Anschluß der Endschalter: Bei optischen Endschaltern sind die Schaltzustände leider nicht so wohldefiniert wie bei mechanischen Endschaltern (kurzschluß nach masse oder pullup direkt am Arduino-Port).
Hier muss die fehlende Entstörung der Eingänge mit einem Tiefpass noch ergänzt werden. Ich habe mir dazu eine kleine Lochrasterplatine zum zwischenstecken zusammengelötet.
Erfolgreich war ein Serienwiderstand von 1,8 Kiloohm und ein Keramikvielschichtkondensator zu 100nF nach Masse. Ohne den Tiefpassfilter wurden die Endschalter bei laufenden Motoren häufig willkürlich als ausgelöst erkannt, obwohl gar keine Auslösung bestand und die Lichtschranke nicht unterbrochen wurde. Offenbar ist in der Repetier-Firmware auch keine Software-Entprellung „eingebaut“ und jeder kleine eingestreute Transient lässt den Eingang kippen.
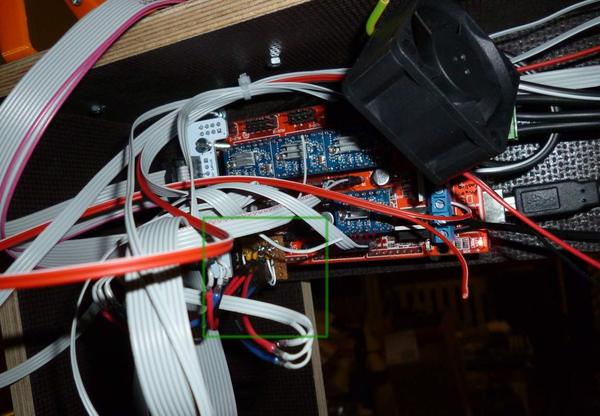
Beim Verlängern der Leitungen habe ich ja Flachbandkabel eingesetzt. Um Störungen zwischen den Motorleitungen zu den Endschalterleitungen zu vermeiden habe ich eine Ader dazwischen freigelassen, was jedoch ohne den Tiefpass am Ramps nicht ausreicht, um einen ordentlichen Betrieb zu erreichen :/
Pololu A4988 Schrittmotortreiber
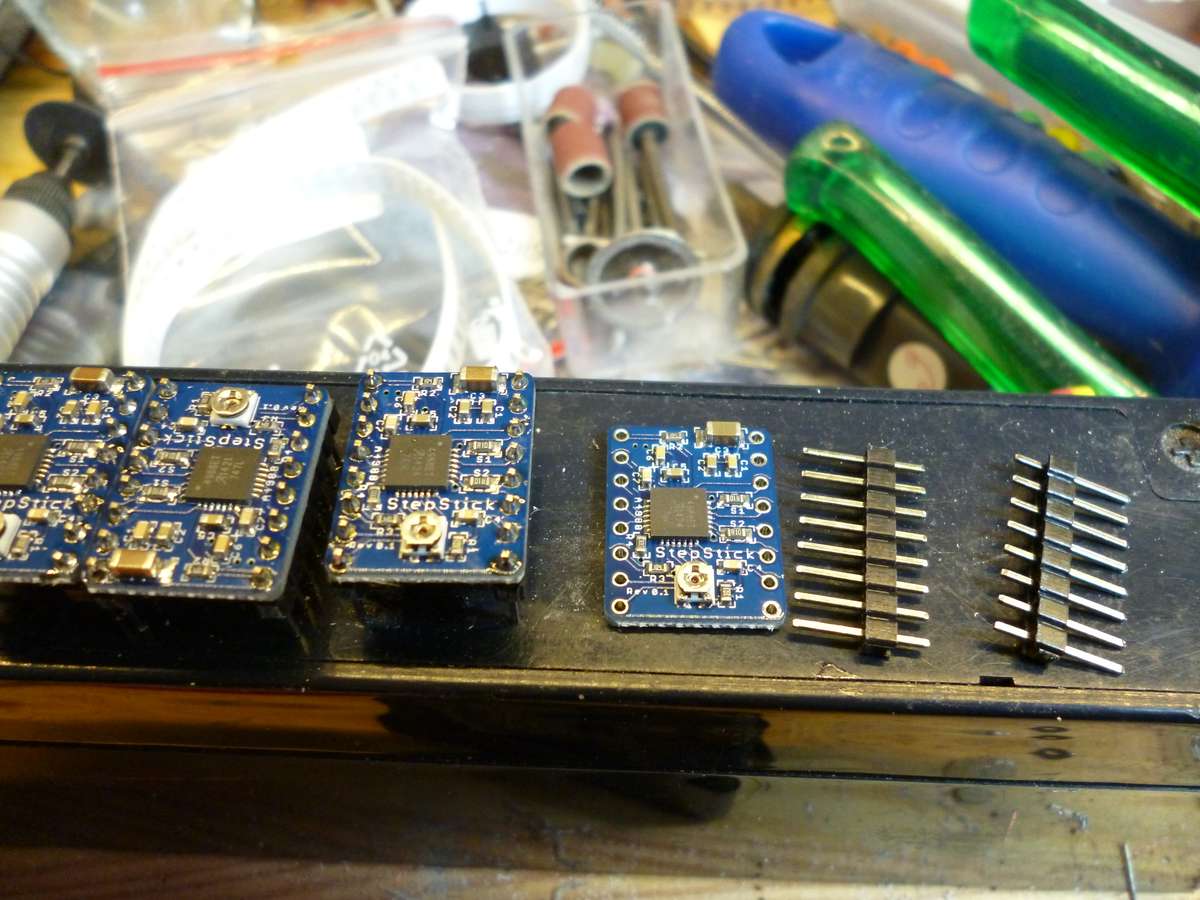
Die Motortreiber kamen bis auf die Stiftleisten vollständig aufgebaut bei mir an, ich musste also nur die Leisten noch anlöten.
Am Poti kann man den Motorstrom einstellen. Mit dem Uhrzeigersinn wird der Strom größer.
Die Referenzspannung kann man mit einem Spannungsmesser direkt am beweglichen Teil des Potis erfassen und gegen Masse messen.
Die Referenzspannung muss entsprechend dem zulässigen Motorstrom der verwendeten Schrittmotoren ausgerechnet und eingestellt werden (oder niedriger). Man kann auch die Motortemperatur im Auge behalten und ggf. noch etwas reduzieren.
Geetech Fullgraphic Smart Controller
Der Smart Controller wird nur angesteckt und bekommt seine Daten per I2C vom Arduino. In der Firmware muss entspechend der Controller „Reprapdiscount Full Graphic“ eingestellt sein. Nicht verwechseln mit dem anderen Reprapdiscount smart controller mit 4 zeiligem LCD.
Es gibt berichte, das das Vollgraphikdisplay die Ausführung der Firmware bremsen würde. Die Aussagen sind zum Teil wiedersprüchlich. Ich werde das beobachten.
Kabelwege
Energiekette zur X-Achse:
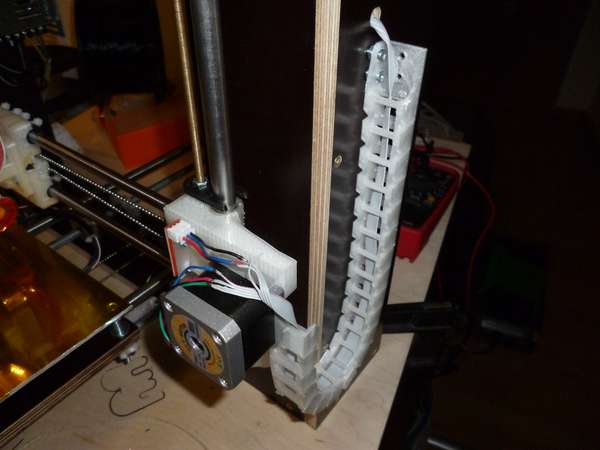
Neben der Energiekette zum Heizbett, kommt auch zur X-Achse eine Energiekette zum Einsatz, um Knickstellen an den elektrischen Anschlüssen zu vermeiden. So werden Kabelbrüche vermieden.
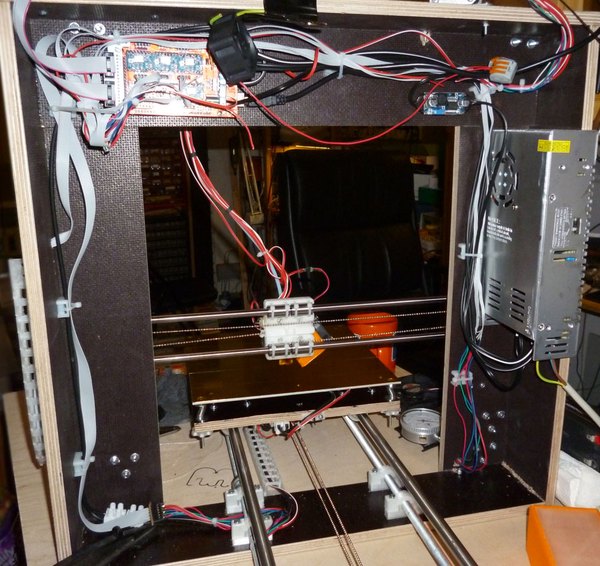
Zum Druckkopf habe ich den Kabelstrang an den Teflonschlauch fürs Filament angebunden, da soll dann später noch solches Wickelband herum, wenn der Kabelbaum komplett ist. Ich habe bereits zusätzliche Leitungen für eine LED-Beleuchtung am Druckkopf und die Lüfter für die Extruderkühlund und die Werkstückkühlung vorgesehen.
Der restliche Kabelsalat verschwindet einfach mit anschraubbaren Kabelbinder-Haltesockeln an der Rückseite der Konstruktion.
Das Netzkabel am Netzteil ist noch ein Provisorium, da muss noch ein Isoliergehäuse über die Schraubkontakte und einen Netzschalter hätt ich auch gern. Ob ich noch einen Kaltgeräteanschluß dazwischen setze oder das Netzkabel lieber mit einer Zugentlastungsschelle sichere, weiß ich auch noch nicht. Ein festes Kabel kann nicht aus der Buchse rutschen.