Im Beitrag Nummer 7 zur Mechthild Fräse war ja dieses Bild zu sehen:
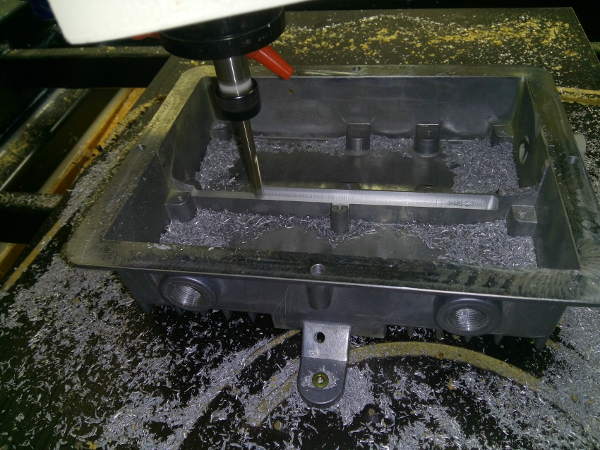
Und ich habe auch bereits verraten, das es für eine LED-Lampe sein soll.
Also mal näher zu dem Thema. Es sind günstige LED-Treiber ICs entwickelt worden, die recht einfach funktionieren: Man schaltet so viele LED-Chips in reihe, bis man der Netzspannung nahe kommt. Dann muss man nur den Strom für eine LED steuern, also ein paar milliampere. Der Chip macht dann einfach nur in linearer Analogtechnik die Strombegrenzung und erwärmt sich dabei, da ja Spannung abfällt. Das kann man nun beliebig weit technisch optimieren, etwa indem man Parallel- und Reihenschaltung im Takt der Sinuswellen des Wechselstromes abwechselt, oder indem man den Peak zum laden eines Kondensators nutzt um die Leds mit der gespeicherten Energie in der fallenden Flanke der Sinuswelle noch etwas nachleuchten zu lassen.
Oder man macht es so billig wie möglich, und lässt die LEDs einfach mit dem gleichgerichteten Wechselstrom im 100Hz Takt mitflimmern, und nebenbei wird das alles dann auch noch dimmbar.
Diese sehr günstige Technik der Stromregelung für LED-Licht hat uns superbillige COB-Led Panels gebracht, die mit Leistungen im zweistelligen Bereich für wenige Euro erhältlich sind. Das muss natürlich auch einmal ausprobiert werden, und manchmal braucht man es irgendwo mal etwas heller, ohne große Anforderungen an die Qualität der Beleuchtung zu haben. Also so ein 50W LED-Keks geordert.
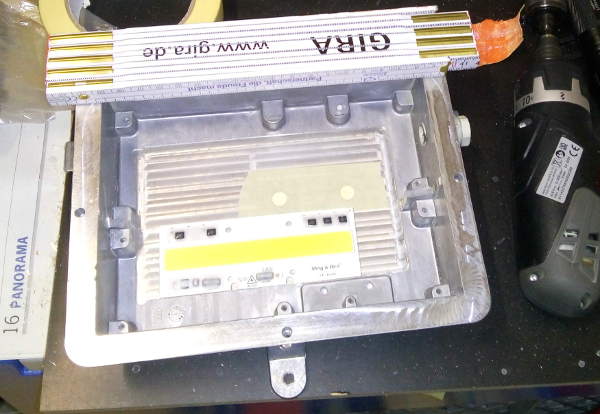
Der Boden/Rückwand vom Gehäuse ist eingeebnet, das Modul habe ich dann probeweise Aufgeschraubt und ausprobiert. Und festgestellt, dass das Kühlrippengehäuse grenzwertig ist, die Gehäusetemperaturen erreichen bereits mit offener Vorderseite 50..55 grad Celsius.
Und was passiert, wenn das Ding umfällt und auf den Rippen zum liegen kommt, und die Konvektion nicht mehr stattfinden kann. Alles nicht schön, so musste also etwas mehr Aufwand in die Sache investiert werden um dem Gerät eine gewissen Lebensdauer zu ermöglichen.
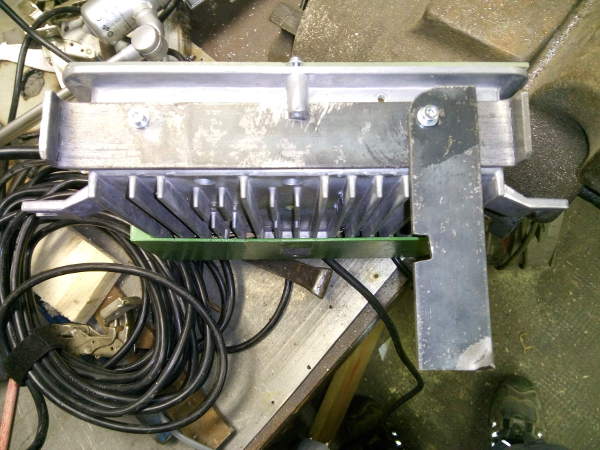
Zunächst hier noch kurz eine Lösung zum Aufstellen, aus zwei Abschnitten Bandstahl, einer an den Enden U-Förmig gewinkelt für zwei äußere Standfüße, und ein schwenkbarer dritter Fuß, der das Leuchtengehäuse nach hinten abstützt.
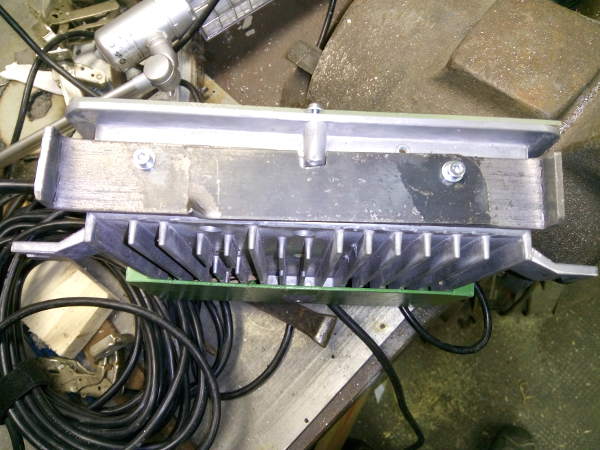
Durch einschwenken des beweglichen Teils wird das ganze Platzsparend.
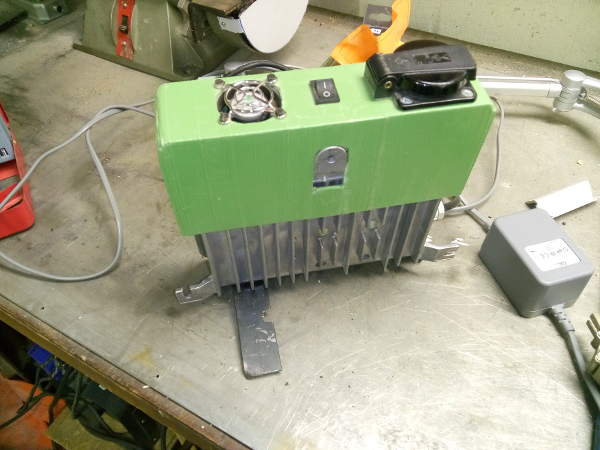
Für das Problem der möglichen Überhitzung habe ich schließlich oben ein Umgehäuse aufgesetzt, welches einen kleinen 40mm Lüfter beherbergt, der immer einen gewissen Luftzug durch die Kühlrippen sicherstellt.
Aus praktischen Erwägungen ist auch ein Schalter für das Licht, und eine Steckdose an Board.
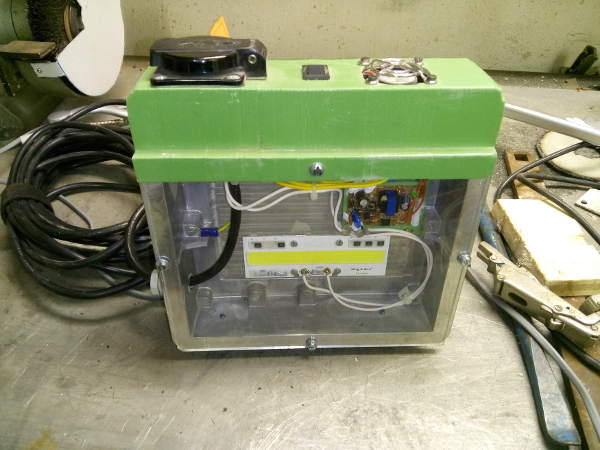
Ein Halterahmen nimmt die Elektronik auf, in diesem Fall besteht die eigentlich nur aus der Stromversorgung für den Lüfter, denn das LED-Modul bringt ja alles für den Betrieb nötige mit. Also fast. Beinahe. Doch dazu gleich mehr.
Komplettiert wird alles mit einer 10 meter langen Anschlussleitung mit angegossenem Stecker, so dass man im Aufstellort flexibel ist, und eine „eingebaute Verlängerung“ dabei ist. Dadurch wird auch klar, was das mit der Steckdose soll.
Doch zurück zur beinahe vollständigen elektrischen Ausstattung. Nach einer Weile fiel nämlich die Schwachstelle der ganze Sache auf: Diese integrierten LED-Treiber sind empfindlich auf Überspannungen. Obwohl am Netzteil ein zusätzlicher Varistor nachgerüstet wurde und die Spannungsversorgung des LED-Panels dort vorbeigeschliffen wird, hat das Abschalten von 3 Leuchtstofflampen mit konventioneller Beschaltung (also Drosseln und altmodischen Leuchstoffröhren) das LED-panel gekillt.
Wie genau es ausgefallen ist kann ich nur mutmaßen, aber vermutlich hat die steile Flanke der Störspannung die Ausregelung durch die LED-Treiberbausteine überfordert und die Led-Chips der LED haben zu viel Strom gesehen. Zumindest wurden mehrere geschädigt, und somit die Reihenschaltungen unterbrochen. Durch die hohe anliegende Spannung hat es noch ein paar mal aufgeblitzt, und die defekten Chips haben sich dann mit schwarzer Verfärbung im Leuchtstoff der weißen LED zu erkennen gegeben. So lange, bis durch die elektrischen Entladungen die Isolation zur Aluminiumplatine beschädigt wurde, und der Fehlerstromschutzschalter dem Spiel ein Ende bereitete.
In der Folge musste ich also ein neues LED-Modul einbauen, und habe ein komplettes C-L-C Entstörfilter nachgerüstet, sowie einen zusätzlichen Varistor direkt an den Lötanschlüssen des LED-Moduls. Seitdem funktioniert das Gerät ohne weitere Ausfälle.
Warum ich das hier soweit ausführe: Man sollte der elektrischen Isolation bei diesen Modulen also nicht allzu weit über den Weg trauen. In jedem Fall empfiehlt es sich, damit zu rechnen das die Rückseite Netzverbindung haben könnte, und entsprechende Vorsichtsmaßnahmen zu treffen. Mein Scheinwerfer ist deshalb als Schutzklasse-1-Gerät aufgebaut, also mit Schutzleiter am Gehäuse. Eine Alternative könnten die neuerdings angeboteten LED-Module mit keramischen Träger sein.