Nach längerer Pause nun zum dritten Teil zur Leiterplattenbohrmaschine. Hier noch ein paar Details zu den restlichen Teilen und der Elektronik.
Um eine Vorstellung der Mechanik zu bekommen, hilft es ganz ungemein, sich die Teile einfach mal so zusammenzusortieren auf dem Monitor. Wenn man dann noch etwas Zeit in das Ausmessen und Nachkonstruieren der Hardware steckt, hat man es nachher einfacher das 3D-Modell einmal „anzuprobieren“ bevor man Mist druckt 🙂
So habe ich mir diese Skizze gemacht und die zubehörteile daran angeordnet. Ich hatte zwischendurch einmal darüber nachgedacht, den Arm mit dem Motor aus mehreren Stücken 20er Vierkantstahlrohr zusammenzusetzen und diese mit dem Schweißgerät zusammenzubraten. Am Ende war es mit Holz dann aber doch einfacher, weil ich (im Dezember als das gebaut wurde) in der warmen Bude bleiben konnte.
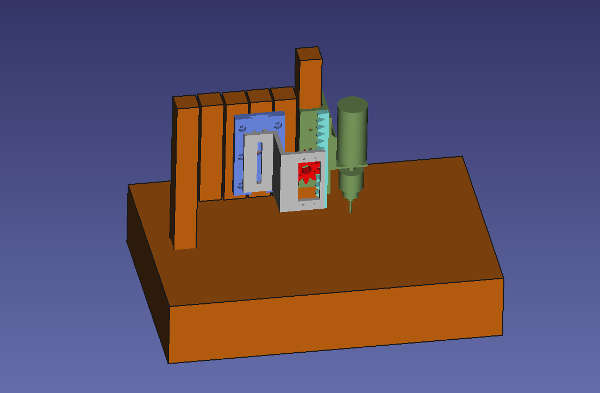
An diesem Bild kann man auch schon sehen, das man an solchen Prinzipmodellen aus ein paar quadern schon ableiten kann, wie z.B. der Halter für den Servo aussehen muss. Durch hinzufügen der bereits fertigen Teile (Zahnstange, Schlitten) hat man virtuell schon einen Zwischenstand bei dem man ein paar Maße nehmen kann, und an den echten Teilen prüfen kann. So steigen die Chancen das die Druckteile gleich beim ersten mal passen.
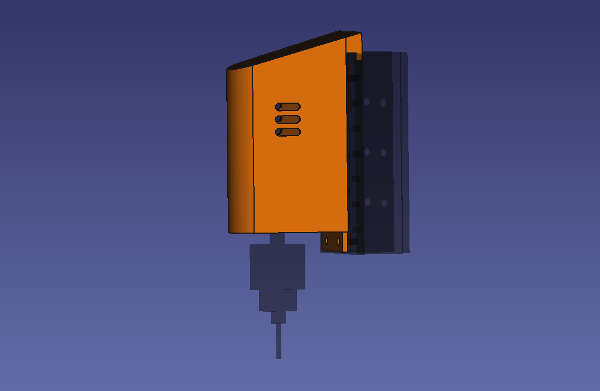
Hier die Motorabdeckung für die Maschine. Das (schwarz-transparente) Teil der bisher fertigen Hardware habe ich importiert (als gittermodell) und dann das benötigte Teil „drumherumkonstruiert“.
Die Flache schräge Oberseite ist beim Drucken die auf dem Druckbett liegende Seite, innen sind noch ein paar minimale Stützstrukturen drin, so das dieses Teil recht einfach und problemlos 3D-Druckbar ist. Gerade bei komplexeren Geometrien hilft es sehr, wenn man sich bei der Konstruktion bereits Gedanken macht in welcher Richtung das gedruckt werden soll, und ein paar entsprechende Anpassungen unternimmt um den Druckvorgang zu erleichtern.
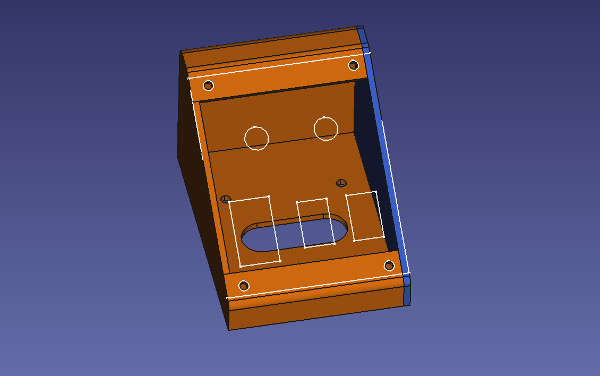
Das ist das kleine Schalterkästchen. Die Seitenwand rechts ist ein Extrateil und wird nachher mit dem restlichen Gehäuse verklebt. Bei diesem einfachen Teil würde es sich auch anbieten es auf der Rückseite stehend zu drucken, aber manchmal denkt man da nicht daran. So in zwei Teilen kann man das linke orangene Teil auf der linken Seite stehend drucken, was sehr einfach ist, und dann die Seitenwand als zweites Teil.
Obendrauf dann die Frontplatte (hier noch als skizze) mit 3 Schaltern und den zwei Löchern für die Poti-Achsen, die dann mit den 4 Löchern in dem orangefarbenem Teil verschraubt wird.
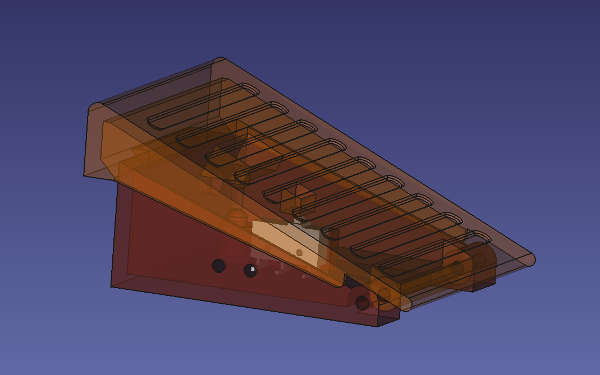
Etwas komplizierter ist der Fußschalter. Ein Klotz mit einem eingebauten mechanisch stabilen Schalter wäre auch gegangen, aber so ist es doch schöner.
Innen wieder ein Abbild der Hardware, hier der Mikroschalter. Links daneben die Nocken für eine Spiralfeder, die den Fußschalter so stark auseinander drückt, das man etwa das Gewicht des Fußes ausgeglichen hat. So kann man längere Zeit damit Arbeiten ohne das der Fuß verkrampft. Am oberen Ende (schlecht zu sehen) ist die Wippe so geformt, das sie einen Anschlag hat.
Zum Zusammenbau werden die Leitungen an den Mikroschalter angelötet, der Schalter mithilfe der beiden Löcher (im Bild vorn) für den Schraubendreher dann angeschraubt, die Feder auf den unteren Nocken gesteckt, das Oberteil oben eingehakt und nachher nur noch unten von beiden Seiten eine Schraube eingeschraubt, die das „Scharnier“ bildet.
Dieses Teil hat auf Anhieb funktioniert.
Nun zur Elektrik: Da sag ich nicht viel dazu, es kommt ein 7,5V Netzteil in den Kasten was ich in meiner Netzteilkiste gefunden habe. Es leistet 4A. Das reicht aus für den Bohrmotor und die Elektronik und das Servo. Wie die Schalter in dem kleinen Pultgehäuse angeschlossen werden kann sich jeder denken. Der große Schaltet alles aus. Die beiden kleinen daneben: Einer schaltet die Luftpumpe zum Spänewegblasen ein, der zweite die obere LED-Beleuchtung.
Die Elektronik ist ein Arduino Pro Mini, ich habe ein Schaltbeispiel aus dem Internet zum Anschluss des Servo verwendet (ja das stammt vom Teebeutelassistent, über den ich noch nicht Berichtet habe, aber manche haben ihn auf dem Fingers-Elektrische-Welt Forentreffen 2016 gesehen) und dort entsprechend hineingekritzelt was da noch so dazu gehört. Den Lautsprecher brauchts nicht, der war nur eben schon auf dem Plan.
Das ganze ist dann auf einem Stück Lochraster zusammengelötet worden, und lässt sich so zusammenfassen: „Es funktioniert so“.
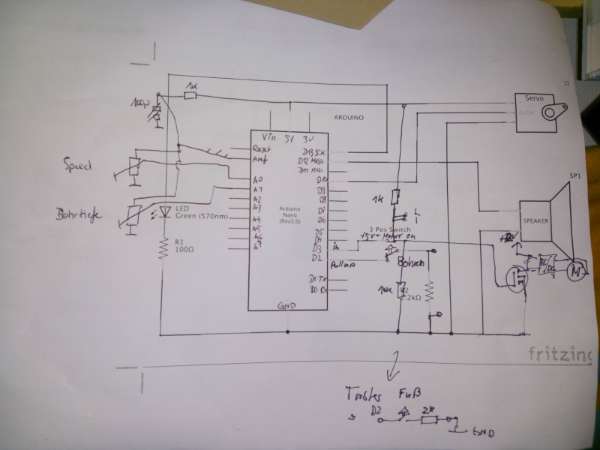
So Ähnlich wie die Elektronik ist auch das Arduino-programm, ich habe davon wenig Ahnung. Ich fasse es auch mal mit „Es funktioniert so“ zusammen.
Im Prinzip sind da ein paar Schleifen mit If-Then-Else Kommandos die im richtigen Augenblick die richtigen Taster-Eingänge abfragen, zwischendrinn mal auf die ADCs mit dem Potis schauen und nebenbei das Servo hin und her fahren lassen.
Mini-Leiterplattenbohrmaschine-Arduino.rar
Als Arbeitstisch habe ich ein Stück Siebdruckplatte verwendet, weil das eine abriebfeste glatte Oberfläche bietet und das positionieren der Leiterplatte damit erleichtert wird.
Als kleines Extra ist in der Mitte eine runde Plexiglasscheibe bündig eingelassen, die von unten über einen Lichtleiter aus Plexiglas mit einer LED beleuchtet werden kann. So kann man ohne Spiegelungen das Lötauge der Leiterplatte gut sehen. Alternativ gibts noch zusätzlich einschaltbares Licht von Oben.
Das fertige Maschinchen funktioniert so:
-
- Werkzeuglängenkorrektur: Man spannt sein Werkstück ein, und dreht das Bohrtiefenpoti auf null. Das Servo fährt den Bohrer dann ganz hinunter. Hat er nicht genug Platz, oder reicht er nicht bis nach unten, muss links an der Seite die Servohalterung mittels Rändelschraube aus der Arretierung gelöst werden, und in der Schwalbenschwanzführung manuell auf die richtige Höhe eingestellt werden.
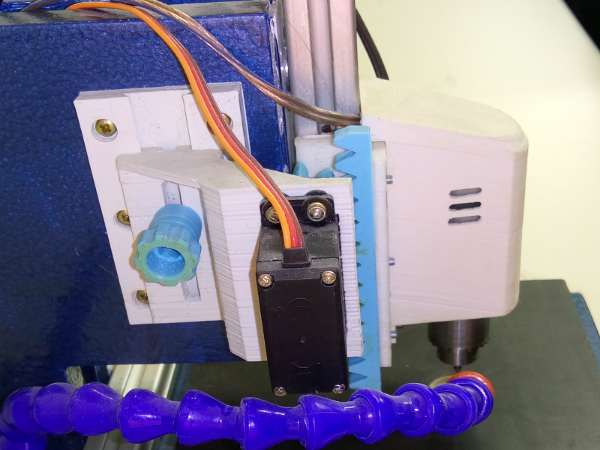
-
- Die Höhe ist richtig, wenn das Bohrtiefenpoti auf Linksanschlag ist, und der Bohrer etwa 2mm unter der Werktischoberfläche endet.
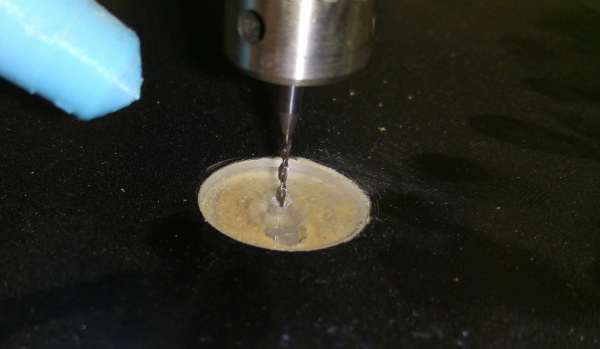
- Nun wird mit dem Bortiefenpoti der Bohrer so weit angehoben, bis er 2mm über der Leiterplatte ist.
- Am zweiten Poti kann die Absenkgeschwindigkeit noch in einem gewissen Bereich der schärfe des Bohrers und Wiederspenstigkeit des Materials angepasst werden.
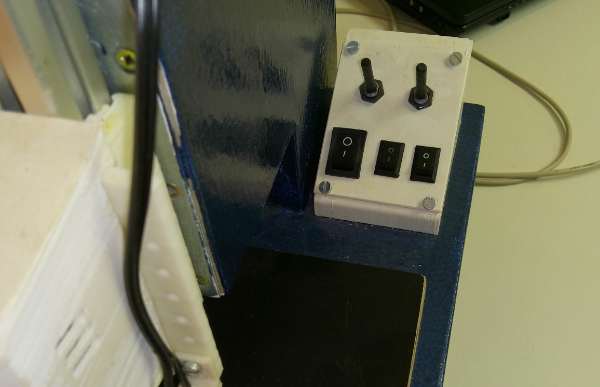
Soweit zur Vorbereitung, dann die zu bohrende Platine auflegen, ein Loch anvisieren und auf den Fußtaster drücken.
Der Motor geht an und der Bohrvorgang beginnt.
Wird der Taster vorzeitig losgelassen, (irrtum, finger, wasauchimmer) fährt der Bohrer sofort zurück nach oben und der Motor geht aus.
Wird der Fußtaster gehalten bis das Loch die endgültige Tiefe erreicht hat, fährt der Bohrer auch zurück in die Ausgangsstellung damit man das nächste Loch bohren kann.
Erreicht der Bohrer die Endposition nicht und fährt vorzeitig zurück, ist der Bohrer stumpf oder die Bohrgeschwindigkeit zu hoch eingestellt. Das Servo wird stumpf angesteuert und nirgendwo kontrolliert, ob es tatsächlich den Weg gefahren ist den es hätte fahren sollen.
Hinweise für Vollhartmetallbohrer: Immer aus dem Vollen bohren, nicht mit einem VHM-Bohrer versuchen bestehende Löcher größer zu bohren.
Für große Löcher kann man aber gut Führungslöcher bohren, und dann mit Akkuschrauber und Spiralbohrer aufbohren (z.B. für 3,5mm Befestigungsschraubenlöcher)