Ich habe auf Youtube folgendes Video gesehen:
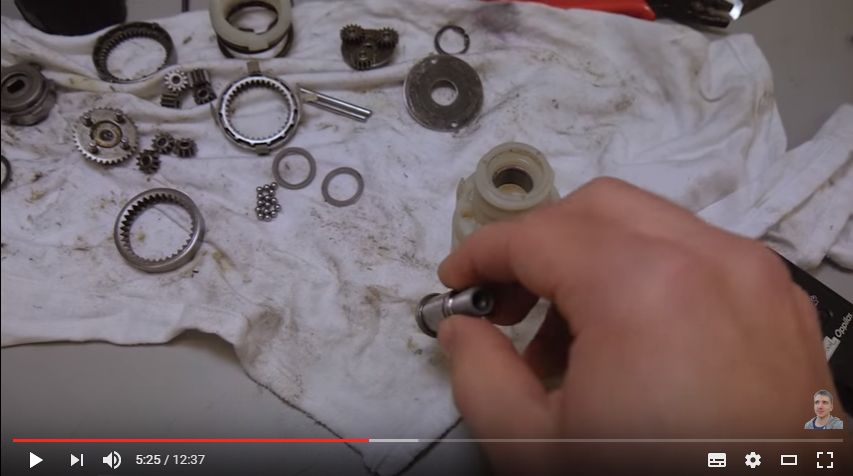
Dieses Video beschreibt das Problem, wenn das Lager der Welle des Bohrfutters abgenutzt ist.
Da mein alter Makita-Akkuschrauber auch so ein Problem hat, und ich im Video bereits das Bronzegleitlager sehen konnte, wollte ich dieses nun austauschen. Vermutlich ist es ein einfaches Normteil, welches nur ausgepresst werden muss, um ein neues einzupressen.
Da das Lagermaterial deutlich weicher als die gehärtete Stahlwelle ist, sollte das eine sehr deutliche Verbesserung bringen, da die Welle selbst kaum abgenutzt sein sollte.
Also habe ich angefangen den Schrauber zu zerlegen, um dann festzustellen das erstmal das Bohrfutter runter muss. Das kenne ich schon, innen ist eine mit Schraubensicherung festgeklebte Linksgewindeschraube in eienr zentrischen Gewindebohrung der Welle, die das auf dem äußeren Rechtsgewinde aufgeschraubte Bohrfutter zuätzlich arretiert.
Also eine typische mechanische Verbindung wo man nur rangeht, wenn es gar nicht anders geht.
Irgendwie habe ich es doch noch los bekommen, und dann den Motor vom Getriebe getrennt, das vordere Teil (Drehmomentversteller) abgeschraubt, und da war der Fehler verschwunden.
Die Welle wackelte nicht mehr.
Also das Ding genauer angesehen. Offenbar hatte sich durch die Gewaltanwendung beim Lösen des Bohrfutters da irgendwas geändert.
Beim genauen Hinsehen (bei mir ist das Teil schwarz) stellte sich heraus, das zwischen dem Getriebe und den beiden Lagern das Konstruktionsteil einmal ringsherum eingerissen war, und durch die ganze Aktion sich das Bruchstück verdreht hatte und festklemmte, weshalb es nun nicht mehr wackelte.
Na so ein Mist, das Lager war völlig in Ordnung, der Halter dagegen gebrochen. Einer der tieferen Stürze von der Leiter muss wohl den Schaden verursacht haben.
Das Teil selbst ist aus Polyamid mit Glasfaserverstärkung.
Mit was klebt man wohl sowas, fragte ich mich. Aber irgendwie ist kleben, nunja, an dieser Stelle, einfach zu leihwändig.
Man müsste es verschweißen. Verschweißen wie man Plexiglas mit einem Lösemittel kleben kann. Oder wie man ABS-Teile mit einer Pampe aus in Aceton aufgelöstem ABS zusammenfügen kann.
Das dauert zwar einige Zeit bis es voll belastbar ist, aber ergibt nach dem zusammenfügen ein Bauteil „aus einem Guß“, welches nachher keine Klebefuge mit einem Fremdmaterial besitzt.
Ob es ein Lösemittel für PA gibt, und noch dazu eines welches einen nicht umbringt oder total saugefährlich ist?
Nun, für einige Dinge gibts spezialkleber. Selbst für PVC und PLA findet man Klebstoffe mit häßlichen Lösemitteln die das Zeug verschweißen. Für PA habe ich nichts dergleichen gefunden. Wohl aber hinweise auf Ameisensäure als Primer.
Weitere Recherche ergab, das sich PA in Ameisensäure auflöst.
Das weckte natürlich meinen Wissensdurst.
So muss man erst einmal feststellen, was Ameisensäure denn so für ein Teufelszeug ist. Es ist stark ätzend, macht ganz häßliche wunden wenn es auf dem Hautgewebe einwirken kann. Es verdampft ätzende Säuredämpfe. Es stinkt stechend. Es kann explosionsfähige Atmosphären erzeugen, allerdings sind die Explosionsgrenzen deutlich handhabungsfreundlicher als bei anderen brennbaren Gasen.
Also eigentlich will man mit so kram nicht wirklich hantieren, aber wenn man entsprechende Vorkehrungen trifft und unter einem Abzug mit entsprechender Vorsicht damit umgeht, ist es handhabbar. Zumindest sind die Dämpfe schon mal kein Gift.
Also versuch macht klug. Behälter aus PP/PE sind offenbar resistent gegen den Stoff. Also habe ich eine Kleinmenge umgefüllt. Da keine passende Pipette zur Hand war, tat es auch eine Einwegspritze, haptisch scheint das ebenfalls PP/PE zu sein. Erste Überraschung: Ja, der Spritzenkörper schon, die schwarze Dichtung nicht. Die hat etwas ausgefärbt. Den kurzen Moment war es aber tolerierbar.
Außer dem Behälter und dem Lösemittel braucht es noch mehr, nämlich etwas Kunststoff zum Auflösen.
Aus Erfahrungen mit dem System ABS und Aceton weiß ich, das die Einwirkdauer von aufgepinseltem Lösemittel viel zu kurz ist, um die Oberflächen so vorzubereiten, das einfaches zusammenfügen nach dem Auftragen eine tragfähige Verbindung erzeugt.
Viel besser ist es, erst etwas Polymer aufzulösen und damit eine mäßig flüssige Lösung herzustellen, die auf die Fügestelle aufgetragen wird. Danach muss man dafür bis zum Ausgasen des Lösemittels die Lage der Teile zueinander fixieren, um ein wiederablösen zu verhindern.
Da sich dieses Konzept bereits bei schwierigen Bruchstellen bewährt hat, habe ich es auch hier angewandt.
Als Material muss dann natürlich etwas PA oder Nylon her. Nur was hat man denn so zur Hand, was aus Nylon besteht. Das erste was mir einfiel war Rasentrimmerschnur. Später bin ich dann noch auf eine weitere ergibige Quelle gestoßen: Die abgeknipsten Enden von Kabelbindern aus Nylon.
Zur schnelleren Auflösung habe ich 10cm Faden in ca. 50 Fragmente zerschnitten und dann in die Säure gelegt.
Nun löst sich das PA in der Säure noch deutlich langsamer als ABS in Aceton, hier ist Geduld gefragt.
Also in einer Viertelstunde ist da auf jeden Fall noch nichts zu erreichen.
Irgendwann war es dann soweit, das ich eine Lösung in der passenden Konsistenz hergestellt hatte.
Der Spalt mit dem Bruch wurde zunächst mit einem Pinsel direkt mit Ameisensäure benetzt, die Kapillarwirkung tat das nötige. Etwas bewegen um das Lösemittel zu verteilen. Danach Auftragen des aufgelösten Polymers auf den Spalt.
Es ist wichtig, nicht zu dicke Schichten aufzutragen, damit sich im aufgetragenen Material keine Blasen bilden. Mehrere dünne Schichten nacheinander ist kein Problem.
Um die Härtung zu beschleunigen habe ich vorsichtig mit etwas Wärme nachgeholfen:
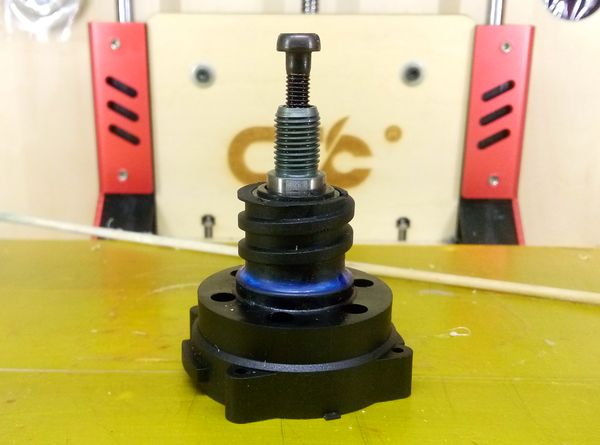
Das blaue Material ist das aufgetragene Polyamid nach der Aushärtung. Blau deshalb, weil des aufgelöste PA blau gefärbt war.
Nach ein paar Tagen zur vollständigen Durchhärtung habe ich alles wieder zusammengesetzt. Wenn man eine nicht so stark belastete Verbindung herstellen/reparieren möchte, ist vermutlich das wiederholte Auftragen nicht wichtig. Ich wollte jedoch die Fügestelle noch durch aufbringen von zusätzlichem Material verstärken, da mein aufgebrachtes Material im Gegensatz zum Originalteil nicht Glasfaserverstärkt und somit weniger belastbar ist.
Das ist jetzt alles zwei Wochen her.
Einige male habe ich den Schrauber inzwischen benutzt zum bohren und schrauben, und bisher ist der Eindruck gut.
Wirklich empfehlen kann ich dieses Verfahren nicht. Einerseits ist Ameisensäure nicht so lustig, andererseits dauert es sehr lange bis das Teil wieder benutzbar ist, da man warten muss bis das komplette Lösemittel langsam aus dem Material herausgewandert ist. So lange ist es auch nicht ungefährlich die Klebestelle zu berühren.
Es ist machbar, aber ob man das unbedingt will hängt wohl vom Wert des zu reparierenden Teils ab.